BACKGROUND
A specialty pipe fabricator in Texas had the perfect storm. Sales had increased, out pacing its production capabilities. This created a bottle neck in their blast room. The client reached out to BlastOne to find a solution that incorporated its existing blasting and painting facility. Additionally, they wanted the new facility to be low maintenance and high productivity
OBJECTIVES
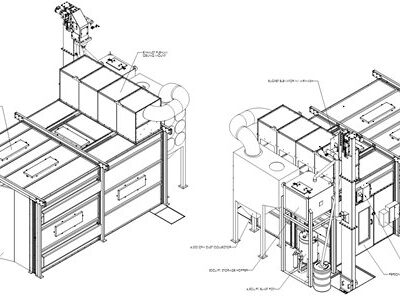
BlastOne designed a solution that incorporated a pre-engineered blast room shell sizing of 10’H x 12’W x 20’L. The blast room had a custom, high-efficiency rated full floor recycling equipment renowned for its low maintenance operation. It could recycle both GL40 steel grit and garnet abrasives. Having this flexibility provides our client the option to take on new projects blasting steel structures and aluminum.
RESULTS
The customer commented, “I would like to take a moment and compliment the install crew on an excellent and professional installation. It has been a pleasure working with him and his crew; he deserves a pat on the back for a job well done.”
We completed installation in less than a week. There was no interference to production.
This new blasting facility will allow this customer to continue to expand in the gulf region. Finally, they no long suffer from blasting bottlenecks and equipment breakdowns that halt production.
KNOWLEDGE & LEARNING
5 CRITICAL COMPONENTS OF A BLAST ROOM
BLAST ROOM PREVENTATIVE MAINTENANCE
BLAST BOOTH RECLAMATION SYSTEMS
CASE STUDIES
Contact BlastOne
We love to talk to customers and help them make the best decisions when purchasing equipment.
You can reach us via our Live Chat, Email, Phone, and Online Form.