COMPANY BACKGROUND
CS Wind Corporation is a wind tower manufacturer with global expertise, reliability, and quality. Their mission is: “We create a bright future for humans and nature.”
WHY CS WIND CHOSE BLASTING ROBOTICS
CS Wind searched for an effective method to abrasive blast the externals of new wind tower sections.
Other options considered for this project included wheel blasting technology. However, as a result of the high standards for surface cleanliness and roughness, wheel blasting was no longer an option. CS Wind chose Blastman Robotics as the partner for blasting automation.
PROJECT OBJECTIVES
Abrasive blast wind tower sections, fast, consistently and with minimum human labor intervention while maintaining the required specifications cleanliness and roughness that allowed the subsequent coating system to last for years.
Advantages of Automated
Considerable savings in production costs
Increased production capacity
Remarkable healthy and safety implications
Freedom to use any abrasive material
Desired surface cleanliness and roughness
Slight surface shaping by controlling the blast pressure
Working lifts and platforms are not needed
Increased fatigue strength of specific welded joints
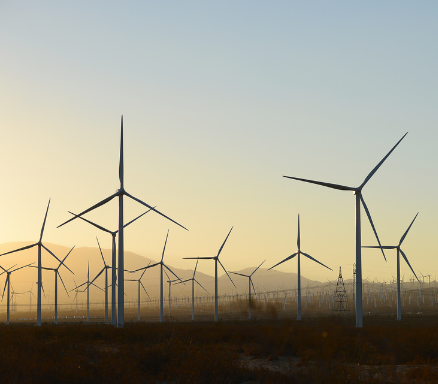
SOLUTION
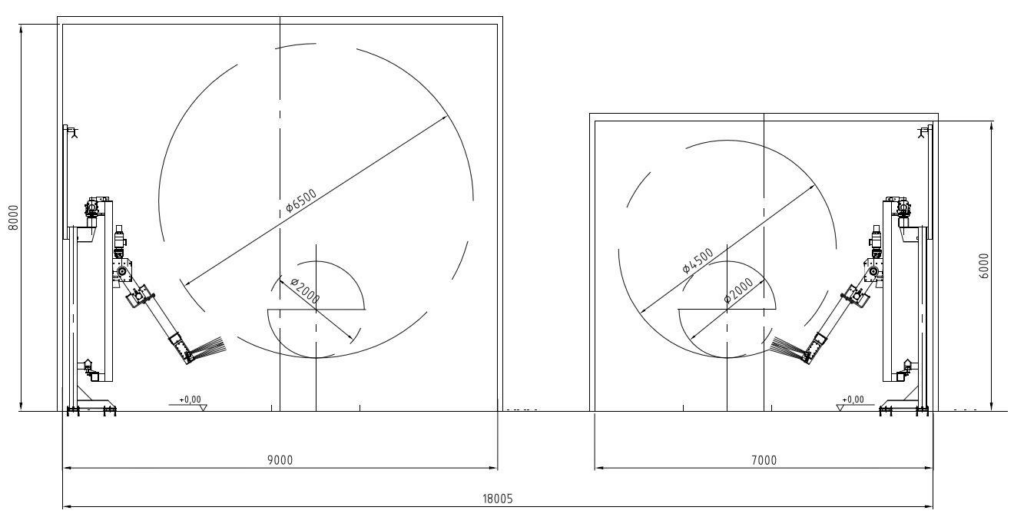
CS Wind installed three surface treatment lines comprised of an abrasive blasting chamber and a painting room. Subsequently, each abrasive blasting chamber has one Blastman B12 robot with two ¾” nozzles.
The Blastman B12 Blasting Robot is mounted to tracks on the wall and has a 4-axis arm that can extend and swivel easily. Meanwhile, each arm supports two large blast nozzles. Typically, this robot works best on simple structures like wind towers.
Firstly, we considered material handling. We used specialized product carts. This system contains in-ground tracks and purpose-built rollers to position the tower section precisely.
Moreover, the robot is programmed to coordinate the rolling of the tower in conjunction with the blast nozzle. In this facility, blasting is done sector by sector: the robot moves from one end to the other, where the roller bed rotates the tower element. This leaves a slight overlap on the blasted sector before the robot returns. Concurrently, the tower element rotates around.
RESULTS
Markedly, CS Wind’s facility is a highly productive wind tower finishing facility in North America. Their blast cleaning capacity with the robots is over 2500 ft2/hr. Chiefly, this is 10x the speed of typical manual blasting.
The resulting surface cleanliness and profile met the required standards using steel grit. However, CS Wind can switch abrasives quite easily if needed. Generally, this flexibility gives CS Wind more long-term versatility for their facility.
Overall, robot programming gives degrees of freedom with five operational modes, including the roller bed rotation parametric and point-to-point Automatic or joystick drive for manual touch-up or programming.

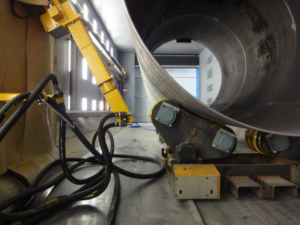
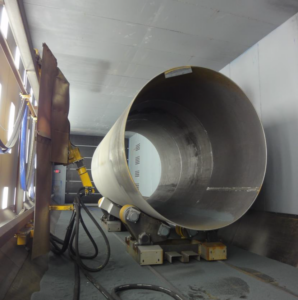
ROBOTIC ABRASIVE BLASTING MYTHS
THE TRUTH BEHIND COSTS, EXPERTISE NEEDED, RANGE OF APPLICATIONS AND FACILITY REQUIREMENTS FOR BLASTING ROBOTS
CASE STUDIES
Contact BlastOne
We love to talk to customers and help them make the best decisions when purchasing equipment.
You can reach us via our Live Chat, Email, Phone, and Online Form.