ExxonMobil, a global refinery, was stuck looking for solutions to ensure they complied to the latest OSHA noise exposure regulations and needed to lower the overall dB level while abrasive blasting. Current OSHA regulations only allow operators to blast for a limited time at standard noise exposure limits. The impact of implementing this time restriction would have meant blasters would have to cut back their daily blasting hours from 6.5 to 5, which would have blown out job timelines, or drastically increase the cost of completing the projects with more workers.
Superior know how
Snakebite XQ saves ExxonMobil unprecedented asset downtime
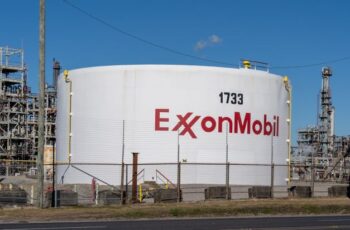
“The implication of the new regulations would have drastically blown out timelines”
Eric – ExxonMobil Chief Industrial Hygienist
SnakeBiteXQ sound trial conducted onsite at ExxonMobil
BlastOne’s Snakebite XQ blast nozzle tests were conducted using GMA ToughBlast Garnet and maintaining between a range of 85 to 110psi. Through extensive trials the XQ delivered a fantastic 90% reduction in noise levels.
“I was standing outside the tank and all I could hear was the compressor. I peeked my head in to see when the blasting would start… and it already had.”
Eric – ExxonMobil Chief Industrial Hygienist
Sound Test Results
Blast Nozzle Used | At Blaster | 25ft from Blaster | |
Regular Tungsten Carbide #7 Blast Nozzle | 122.3 dBA | 109.8 dBA | |
SnakebiteXQ #7 Silenced Blast Nozzle | 101.9 dBA | 91.8 dBA | |
Sound Reduction Recorded | 20.4 dBA | 18 dBA |
Summary
With the introduction of the SnakebiteXQ we no longer need to monitor for extra noise exposure when blasting. Additionally, other trades can work in the same vicinity as the blasting contractor without wearing heavy hearing protection. Using GMA ToughBlast Garnet we now can also blast faster, use less abrasive with no heavy metal concerns, and save money.