OVERVIEW
Our client approached us looking for a solution to a project involving the removal of epoxy coating from steel fuel storage tanks.
Foremost, they wanted to offer a solution to the facility owner, showing a safer blasting method without compromising productivity.
The epoxy coating had an average thickness ranging from 275 microns to 300 microns. Additionally, it was in poor to fair condition.
Previously, the contractor had stripped the tanks on this site using a manual dry abrasive blasting process in which the blasting operator worked from a boom lift. Using the dry blasting, production rates for removal of the old coating were typically in the 15-25 m² per hour range.
SUGGESTED PROPOSAL
VertiDrive Multi Purpose Robots
For this application, we recommended the VertiDrive M4 convertible system. The VertiDrive M4 enables UHP waterjet blasting and can be reconfigured for open abrasive blasting.
The coating is removed rapidly with UHP water jetting. Subsequently followed by abrasive blasting to create the required profile.
SIMULATED TRIAL
In advance, we prepared a section of the tank wall. Secondly, we blasted the wall to a SA 3 white metal finish with a surface profile of 70 microns. Thirdly, we applied an epoxy tank coating to a dry film thickness of 300 to 320 microns.
Our trial:
1. Captive UHP Waterjet operating at 2800 bar 26 LPM, and
RESULTS
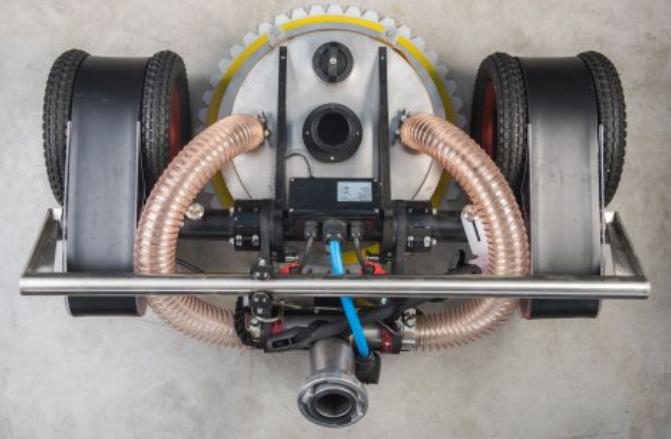
VertiDrive M4 – UHP Configuration
Initially, we tested the VertiDrive M4 UHP configuration. We used a Vermeer trailer-mounted vacuum system for vacuum extraction.
During UHP usage, we calculated the paint removal rate to be 49 m²/hr on a straight run stripping a 400 mm wide path.
However, maneuvering time for subsequent runs reduced the overall production rate to an average of 41 m²/hr.
The resultant finish of an SSPC SP WJ 1 Waterjet standard flash rust was not noticeable in the 2 hours following the trial.
CONCLUSION
In conclusion, we reduced abrasive consumption by 80% by switching to UHP blasting. Additionally, production increased by 20%.
CASE STUDIES
Contact BlastOne
We love to talk to customers and help them make the best decisions when purchasing equipment.
You can reach us via our Live Chat, Email, Phone, and Online Form.